Executive Summary
The PTFE packing industry has evolved significantly since its inception, driven by advancements in chemical processing, oil & gas infrastructure, and renewable energy systems. By 2025, the global market is projected to reach $1.8 billion, growing at a CAGR of 6.2% from 20242. 2025 global PTFE packing industry whitepaper provides a granular analysis of PTFE packing classifications, technical specifications, and industrial applications, focusing on eight specialized product categories critical to modern sealing solutions.
1. Market Overview
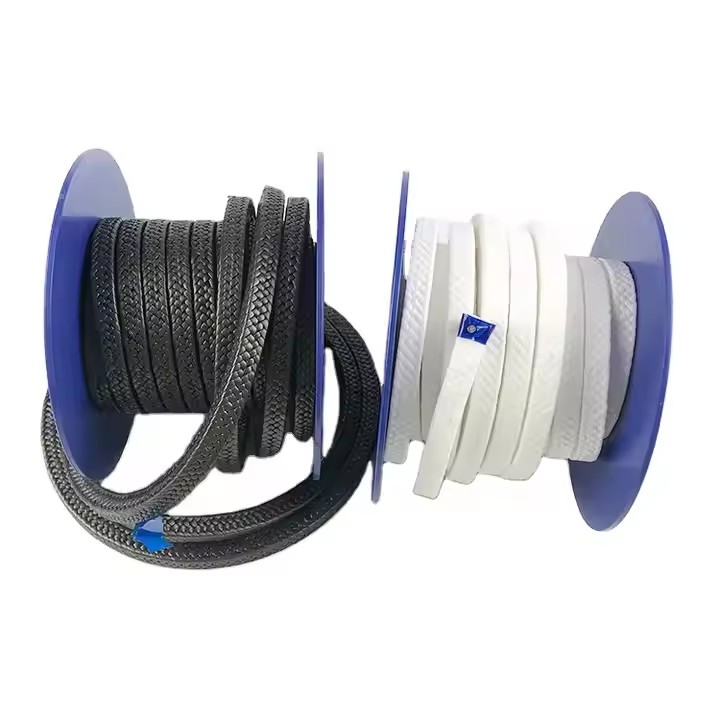
2025 Global PTFE Packing Industry Whitepaper
1.1 Industry Growth Drivers
- Demand Surge in Oil & Gas: PTFE packing is indispensable for sealing valves and pumps in offshore drilling, where corrosion resistance (pH 3–12) and pressure tolerance (up to 3,000 psi) are critical.
- Renewable Energy Adoption: Wind turbine hydraulic systems and hydrogen fuel cell plants require High-Temperature PTFE Graphite Gland Packing to withstand cyclic thermal stresses (operating range: -100°C to +315°C).
- Regulatory Compliance: Non-asbestos formulations dominate due to OSHA and EU Directive 2009/148/EC mandates, phasing out carcinogenic materials.
1.2 Regional Dynamics
- Asia-Pacific: Accounts for 42% of global consumption, led by China’s chemical manufacturing hubs and India’s refinery expansions.
- North America: Emphasis on Wear Resistance PTFE Packing for shale gas extraction, with a 15% YoY growth in valve sealing applications.
2. PTFE Packing Classifications & Technical Specifications
2.1 Aramid Fiber PTFE Packing
- Composition: Hybrid braid of PTFE filaments (70–80%) and aramid fibers (20–30%) for tensile strength (≥220 MPa).
- Applications: High-speed centrifugal pumps in petrochemical plants, reducing gland friction by 40% compared to traditional flax packing.
2.2 Non Asbestos PTFE Packing with Oil
- Design: PTFE fibrils impregnated with silicone-free lubricants (ISO 12922:2024 compliant) to minimize breakout torque in steam valves.
- Performance: Operates at 25 bar/250°C with leakage rates <0.1 cc/hr, ideal for geothermal power plants.
2.3 White PTFE Gland Packing with Aramid Corners
- Structure: PTFE core wrapped with aramid-reinforced edges to prevent extrusion under pulsating loads (e.g., reciprocating compressors).
- Certifications: FDA 21 CFR §177.1550 for food-grade sealing in pharmaceutical processing.
2.4 Black Graphite PTFE Gland Packing with Aramid Corners
- Material Synergy: Graphite-embedded PTFE (15–20% wt.) enhances thermal conductivity (4.5 W/m·K) for heat dissipation in nuclear reactor coolant pumps.
- Standards: ASME B16.34 for valve stem sealing in LNG terminals.
2.5 High-Temperature PTFE Graphite Gland Packing
- Thermal Resilience: Withstands 400°C intermittent peaks using oxidized graphite layers, reducing maintenance intervals by 60% in glass manufacturing kilns2.
2.6 PTFE with Aramid in Corners Reinforced Braided Sealing Packing
- Mechanical Advantage: Diagonal aramid webbing increases radial load capacity (≥50 kN/m) for shipboard ballast valve systems.
2.7 Wear Resistance PTFE Packing
- Surface Treatment: Laser-etched microgrooves retain lubricants, achieving a wear rate of <0.02 mm³/N·m in abrasive slurry pumps.
2.8 Pure PTFE Pump Gland Braided Packing Without Oil
- Chemical Inertness: 100% PTFE construction (ASTM D4894) for ultra-pure fluid handling in semiconductor etching processes.
Please download the document to view the detailed report!
WhatsApp
Scan the QR Code to start a WhatsApp chat with us.