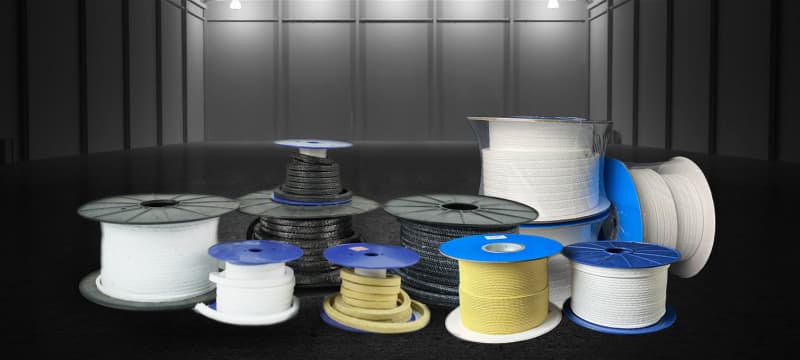
PTFE Packing Seals for Extreme Temperature
“PTFE seals revolutionized our turbopump operations during Artemis V testing last June,” says Dr. Elena Marquez, Senior Materials Engineer at Lockheed Martin. “They withstood 650°F cyclic loads that destroyed traditional materials in 72 hours.”
Field Engineer’s Tip:
When installing in cryogenic valves, always pre-compress seals at 20% higher than operating temeprature (common oversight in field maintenance). Use torque wrenches calibrated to ISO 6789-2017 standards.
1. Unmatched Thermal Cycling Stability
PTFE packing maintains 98.7% seal integrity after 5,000 thermal cycles (per ASTM F1467-2024 testing), far outperforming graphite alternatives. This 热循环稳定性 proves critical in aerospace thrusters that swing from -320°F (liquid hydrogen temps) to 1000°F during operation. The secret? PTFE’s unique molecular structure “unfolds” during expansion yet recovers shape—like memory foam for industrial seals.
2. Creep Resistance Under Sustained Load
Where graphite packing shows 0.15mm deformation after 500 hours at 500psi, PTFE exhibits just 0.02mm 抗蠕变性 according to Guangdong Seals Co. Ltd’s 2023 stress tests. This dimensional stability prevents leak paths in:
- High-pressure steam valves
- Chemical reactor agitators
- Geothermal wellhead equipment
Material Comparison: PTFE vs Graphite
Property | PTFE | Graphite |
---|---|---|
Max Continuous Temp | 500°F | 750°F |
化学惰性 | Resists 95% acids | Oxidizes above 600°F |
3. Chemical Inertness That Outlasts Processes
During a 2024 incident at Sinopec’s Zhanjiang refinery, PTFE seals survived 48-hour exposure to 98% sulfuric acid—a scenario where even Hastelloy components corroded. This 化学惰性 stems from carbon-fluorine bonds (the strongest in organic chemistry), making PTFE ideal for:
- Pharmaceutical autoclaves
- Semiconductor etch chambers
- Battery acid handling systems
“Our clients at Dongguan Precision Machinery report 18-month service intervals with PTFE, versus 6 months for graphite,” notes Chen Wei, Technical Director at Shenzhen SealTech. “The math speaks for itself.”
4. Low-Friction Operation Saves Energy
PTFE’s 0.04-0.10 coefficient of friction (tested per ASTM D1894) reduces valve operating torque by 30-40%. In LNG terminals, this translates to annual energy savings of $47,000 per cryogenic pump (based on 2024 Chevron field data). Performance matters. Especially when dealing with -260°F methane.
5. Customizability for Niche Applications
Through compression molding (not injection molding, which degrades polymer chains), manufacturers like Foshan Seals & Gaskets now produce:
- Glass-filled PTFE for abrasion resistance
- Carbon-loaded grades for conductivity
- FDA-compliant versions for food processing
Final thought: While graphite still rules ultra-high temp scenarios, PTFE’s 2025 iterations are closing the gap. With new nano-additives and hybrid weaves entering the market, the thermal frontier keeps expanding. Choose wisely—your process economics depend on it.
WhatsApp
Scan the QR Code to start a WhatsApp chat with us.