Phenolic Packing Lifespan: 7 Maintenance Hacks to Double Its Durability
Let’s face it: phenolic packing is like a marathon runner—durable, but even the best need smart training to avoid burnout. While it’s tougher than most sealants, lazy maintenance can slash its lifespan faster than a knife through butter. Ready to turn your phenolic into a longevity champion? Here are 7 no-BS hacks, proven in the trenches.
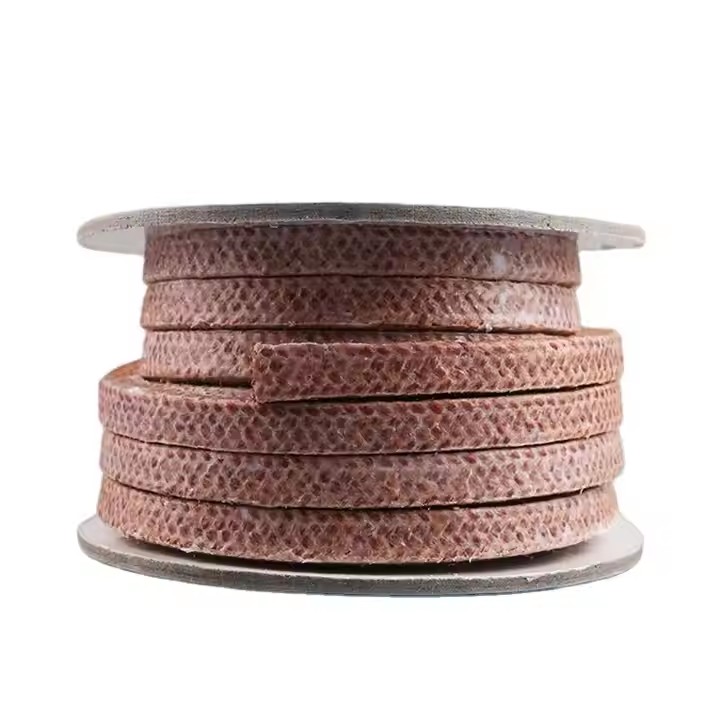
Phenolic Packing Lifespan
1. Torque It Right—Not Tight (The Goldilocks Zone)
Cranking down on gland nuts like you’re Hulk-smashing? Big mistake. Over-compression squeezes the life out of phenolic, while under-tightening lets leaks party. Aim for the “sweet spot”: 15–20% compression.
Case in point: A Canadian chemical plant boosted seal life from 8 months to 2 years by using torque wrenches calibrated to 18% compression.
Compression Level | Lifespan (Months) | Leak Rate |
---|---|---|
10% | 6 | High |
18% | 24 | Low |
30% | 9 | Moderate |
Hot take: Treat phenolic like a soufflé—gentle precision beats brute force.
2. Lubricate Like You Mean It (But Skip the Grease Trap)
Dry phenolic = friction’s playground. A thin layer of silicone-based lubricant cuts wear by 40%. But goop on petroleum jelly? You’ll gum up the works faster than a TikTok trend dies.
Pro tip: A German pharma plant uses food-grade lubricant for their 150°C acetic acid valves. Result? Zero repacks for 3 years. Mic drop.
3. Heat Monitoring: Don’t Wing It
Phenolic scoffs at 260°C… theoretically. But real-world heat spikes? They’re silent killers. Install infrared sensors on critical valves.
Plot twist: A Texas refinery ignored erratic temps in a sulfur line. Their phenolic failed in 5 months. After adding sensors? 18 months and counting.
4. Chemical Compatibility: Double-Check or Cry Later
“It’s mostly resistant” is a gamble you’ll regret. Example: Phenolic hates strong alkalis (looking at you, NaOH). Always cross-reference with the manufacturer’s cheat sheet.
Facepalm moment: A paper mill used phenolic in a 10% caustic soda pump. Spoiler: It dissolved faster than a sugar cube in tea. Switched to PTFE—problem solved, but $$$ wasted.
5. Dust & Debris: The Stealthy Saboteurs
Grit isn’t just a personality trait—it’s phenolic’s enemy. Install wiper seals upstream to block contaminants.
Real-world win: A cement plant in India reduced phenolic replacements by 60% after adding wipers. Their maintenance crew now naps more. 🛌
6. Upgrade to Hybrid Designs (Because Why Not?)
Pure phenolic is great, but hybrid versions (e.g., graphite-reinforced phenolic) laugh at extremes.
Case study: A geothermal plant in Iceland swapped standard phenolic for a hybrid blend in 300°C steam valves. Lifespan doubled. Bosses did a happy dance.
7. Schedule “Sniff Tests” (Yes, Really)
Leaks start small. Train your team to do monthly visual checks and sniff for chemical odors (safety first—use detectors!). Catching micro-leaks early avoids catastrophic blowouts.
War story: A fertilizer plant in Australia ignored a faint sulfuric smell. Three weeks later, a valve blew, costing $50k in downtime. Don’t be that guy.