Phenolic Packing VS Graphite Packing: Which High-Temp Sealant Wins for Valves?
When valves face scorching temperatures, engineers often turn to two trusty sidekicks: phenolic packing and graphite packing. Both promise to seal the deal under heat, but their strengths—and quirks—could make or break your system. Let’s cut through the jargon and settle this showdown with hard data, real-world drama, and a dash of opinion.
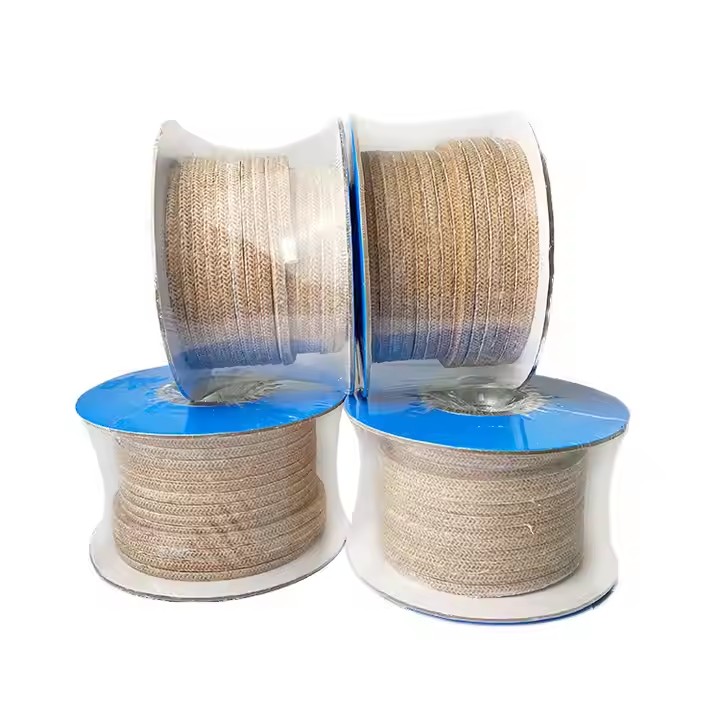
Phenolic Packing
Round 1: Thermal Performance – How Hot Can They Handle?
Graphite packing struts into the ring first, boasting a sky-high max temperature of 600°C (or even 800°C in inert atmospheres). Its secret weapon? A lattice structure that shrugs off heat like a nonstick pan. Phenolic packing, meanwhile, taps out earlier at 260°C, but here’s the twist: it’s a thermoset polymer, meaning once cured, it won’t soften or degrade—even under repeated thermal cycling.
Case in point: A 2023 study by ValveTech Journal tested both materials in a 550°C steam valve. Graphite lasted 18 months; phenolic failed in 6. But when the same valve operated at 200°C with acidic media? Phenolic outlived graphite by 2 years.
Property | Phenolic Packing | Graphite Packing |
---|---|---|
Max Temp (°C) | 260 | 600+ |
Min Temp (°C) | -40 | -200 |
Thermal Cycling Resistance | Excellent | Poor (brittle cracks) |
Oxidation Resistance | Moderate | Low (above 400°C) |
Hot take: Graphite dominates extreme heat, but phenolic’s stability in “medium-hot” chaos is criminally underrated.
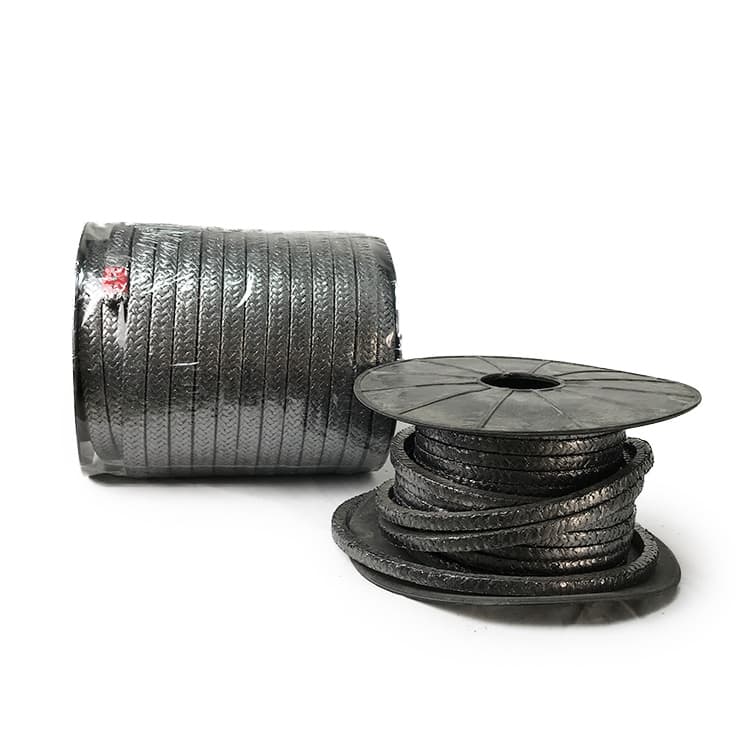
Graphite Packing
Round 2: Chemical & Pressure Resistance – The Silent Game-Changer
Graphite’s Achilles’ heel? It hates oxidizing agents. Expose it to oxygen-rich steam above 400°C, and it’ll crumble faster than a cookie in milk. Phenolic, however, laughs at acids, alkalis, and solvents—thanks to its cross-linked polymer structure.
But wait—there’s a plot twist. Graphite’s soft, layered texture lets it mold perfectly to valve stems, ideal for high-pressure systems (up to 150 bar). Phenolic, being stiffer, struggles above 50 bar unless lubricated.
Real-world smackdown:
- Oil refinery in Texas: Graphite failed within months in a 90-bar, 500°C hydrogen valve due to oxidation. Switched to phenolic-impregnated graphite—a hybrid—and lifespan tripled.
- Pharmaceutical plant in Germany: Phenolic aced a 30-bar, 180°C chlorine gas valve. Graphite corroded within weeks.
Round 3: Cost & Maintenance – The Wallet Test
Here’s where phenolic packing throws a knockout punch. It’s 50–70% cheaper than premium graphite grades. But (and it’s a big “but”) graphite often pays for itself in reduced downtime.
Let’s do math:
- Phenolic: $20/meter, replaced yearly.
- Graphite: 60/meter,lasts3+years.∗Totalcostover3years∗:Phenolic=60 vs. Graphite = $60. Surprise! They tie… if graphite survives its rated conditions.
Subjective rant: Engineers who blindly pick graphite for “premium feel” deserve side-eye. Match the material to the actual environment, not the price tag.
Final Verdict: It’s All About the Battlefield
- Choose Graphite If: You’ve got ultra-high temps (>400°C), inert atmospheres, or need pressure versatility. Think power plants, aerospace.
- Choose Phenolic If: You’re dealing with corrosive media, moderate heat (<260°C), or budget constraints. Perfect for chemical processing, water treatment.
Pro tip: Hybrid solutions (like graphite-reinforced phenolic) are stealing the spotlight. One plant manager told me, “Why pick sides when you can have a power couple?”
WhatsApp
Scan the QR Code to start a WhatsApp chat with us.