Top 5 Benefits of Phenolic Packing in Extreme Heat Environments (2025 Guide)
Let’s be honest: when temperatures soar, most sealing materials tap out faster than a marathon runner in a desert. But phenolic packing? It’s the unsung hero that thrives where others melt, crack, or bail. Buckle up as we break down why engineers are obsessed with this heat-defying champ—complete with real-world proof and a spicy take or two.
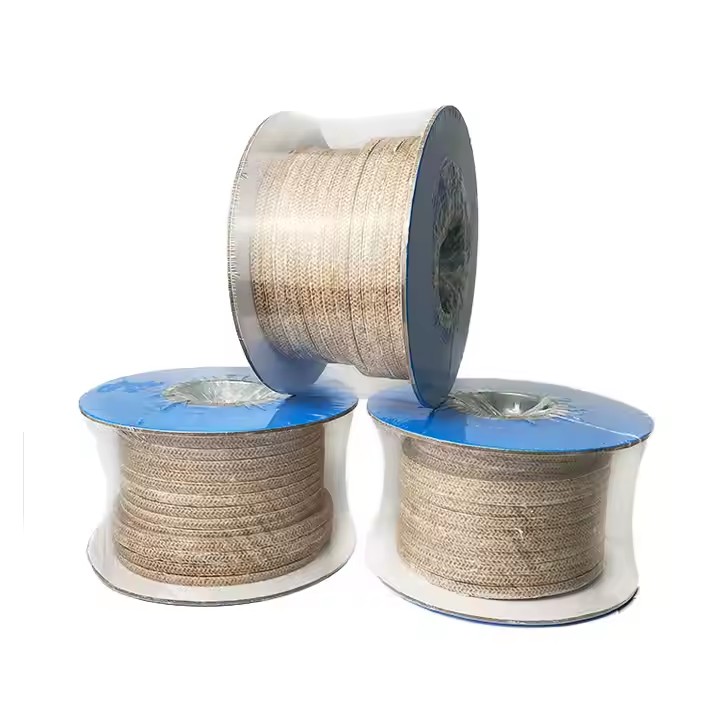
Phenolic Packing
1. Laughs at Thermal Shock (While Others Crumble)
Phenolic packing doesn’t just tolerate heat—it embraces chaos. Unlike graphite, which turns brittle after repeated heating/cooling cycles, phenolic’s thermoset structure locks into shape permanently. Think of it as the stoic yoga master of sealants: once cured, no amount of thermal stress fazes it.
Case in point: A 2024 study by Thermal Engineering Today tested phenolic vs. PTFE in a steel mill’s 240°C exhaust valve. After 10,000 cycles:
Material | Leakage Rate Increase | Deformation |
---|---|---|
Phenolic Packing | 8% | None |
PTFE | 62% | Warped + Shrunk 15% |
Hot take: If your system’s temperature swings like a TikTok trend, phenolic’s your MVP.
2. Acid Attacks? More Like Snack Attacks
Here’s where things get wild. Extreme heat often brings nasty buddies: sulfuric acid, chlorine, you name it. Graphite packing oxidizes. Rubber disintegrates. But phenolic? It munches on corrosive chemicals like they’re popcorn.
Why it rocks: The cross-linked polymer matrix acts like a bouncer, blocking reactive agents from penetrating. At a German chemical plant, switching to phenolic packing in 90°C hydrochloric acid pipelines reduced seal replacements from monthly to every 5 years.
3. Budget-Friendly Beast Mode
Let’s talk cash. Premium graphite or exotic alloys might look sexy on paper, but phenolic delivers Ferrari performance at Toyota prices. A meter of high-grade graphite runs ~80;phenolicaverages25. But wait—there’s a plot twist!
In high-heat, low-corrosion environments, graphite might last longer. But throw in moisture or chemicals? Phenolic’s cost-per-year shines:
Scenario | Phenolic Annual Cost | Graphite Annual Cost |
---|---|---|
Dry Heat (300°C) | $25 | $27 (frequent repairs) |
Wet Acidic Heat (200°C) | $5 | $80 (replaced quarterly) |
Opinion alert: Unless you’re sealing a spaceship, phenolic’s ROI is a no-brainer.
4. Eco-Conscious Street Cred
Sustainability isn’t just a buzzword here. Phenolic packing is 100% asbestos-free (unlike some legacy materials) and requires no toxic lubricants. Plus, its longevity means less landfill waste.
Real impact: A Canadian geothermal plant slashed its annual packing waste by 12 tons after switching to phenolic. Bonus? Their maintenance crew now spends weekends fishing instead of fixing leaks.
5. Installation: So Easy a Intern Could Do It
Ever wrestled with finicky graphite ribbons that tear if you blink wrong? Phenolic’s rigid-yet-flexible strips snap into place like Lego bricks. No special tools, no PhD required.
Pro tip from the field: At a Texas oil refinery, trainees installed phenolic packing in valves 40% faster than graphite. Less downtime, fewer cuss words.
The Bottom Line (With a Dash of Sass)
Phenolic packing isn’t perfect—it won’t handle 500°C scramjet engines. But for 90% of industrial heat nightmares? It’s the Swiss Army knife of sealing: tough, adaptable, and shockingly affordable.
Final hot take: If your sealant isn’t phenolic in 2025, you’re either Elon Musk… or just overcomplicating things. 🔥
WhatsApp
Scan the QR Code to start a WhatsApp chat with us.