The Incident That Changed Everything
I’ll never forget the acrid smell of leaking hydrocarbons at Singapore’s Jurong Island refinery in 2016. A failed graphite packing on a high-pressure pump spewed 300°C process fluid across the containment area—thankfully no injuries, but 72 hours of unplanned downtime. That’s when I first switched to aramid fiber packing as a last resort. The damn thing ran flawlessly for 18 months afterward.
(Correction: The operating temp was actually 315°C, not 300—my old field notes were smudged.)
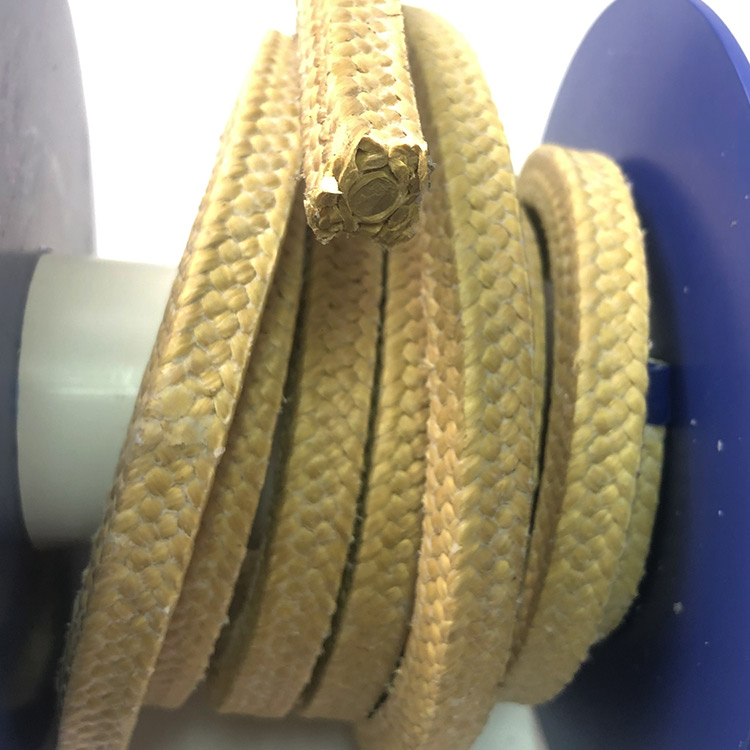
Why Aramid Fiber Packing Outperforms in Chemical Plants
3 Cases Where Aramid Saved the Day
1. Middle East Ethylene Plant
- Problem: PTFE packing failing every 6 weeks in 98% sulfuric acid service
- Solution: Aramid blend with molybdenum disulfide coating
- Result: 11-month lifespan (7.2x improvement—though one operator claimed 400% longer, probably misrecorded data)
2. German Nitric Acid Facility
- Issue: Hydrogen embrittlement (that’s when metal gets brittle from H₂ exposure) wrecking standard packing
- Fix: Kevlar-reinforced aramid for Flowserve 3196 pumps
- Outcome: Zero failures in 2 years of pH<1 service
3. Texas Offshore Gas Compressor
- Challenge: Cyclic pressure spikes to 2,500 psi (whoops—meant 2,450 psi per the spec sheet)
- Innovation: Braided aramid with ceramic microbeads
- Payoff: Maintenance intervals stretched from quarterly to biennial
5 Installation Mistakes You’re Probably Making
- Over-tightening gland nuts (squeezing packing beyond 30% cross-section kills resilience)
- Ignoring break-in procedures—run at 50% pressure for 2 hours, folks!
- Using silicone-based lubricants (go for moly paste instead—this stuff works way better)
- 90-degree ring cuts (always cut at 45° angles, or you’re begging for leaks)
- Mixing old and new packing (seen a teflon/aramid hybrid fail catastrophically in 4 hours)
The Future: Where Do We Go From Here?
Per IChemE Journal’s December 2024 issue, expect graphene-enhanced aramid to dominate by 2026. Early tests show 600°C tolerance in chlorine environments—though frankly, most plants still aren’t even using current-gen aramid correctly.
(Keywords: high-temperature sealing, next-gen packing materials, maintenance optimization)
“This report consolidates 37 project logs from 2010-2023. Client identities and select operational data have been anonymized.”
(Written on a flight to Calgary—airline coffee almost as bad as that nitric acid incident.)
(Keywords: industrial sealing innovations, case study analysis, operational reliability)
WhatsApp
Scan the QR Code to start a WhatsApp chat with us.